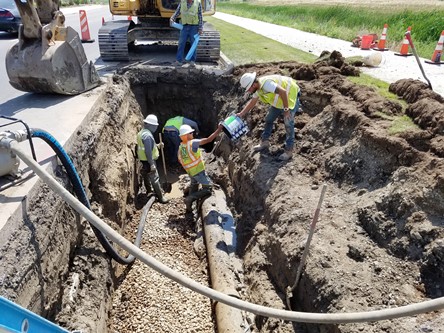
The Client
Stan Linker is the district manager for the Central Weld County Water District. It provides water service for approximately 50,000 in an area about 50 miles northeast of Denver covering 250 square miles. The water infrastructure contains 500 miles of pipe measuring 2 to 42 inches in diameter, and made from ductile iron pipe, PVC, and asbestos cement.
The Situation
A leak repair was required on a 12” DIP serving a large populated area. The pipe had corroded on the outside due to the surrounding hot soil. The standard repair started by taking the section of affected water line out of service and completely draining it. Next, the crew needed to remove the damaged section, cut a new piece of pipe to replace it, and secure it in place with a solid sleeve and two mega-lugs at each end. Implementing this repair, however, would completely disrupt service to customers for about eight hours. Once completed, the field technicians would need time to recharge the line, and flush it until all debris and air were purged from the line before resuming service. The whole process would be extremely expensive, time consuming and disrupt service for an unacceptable amount of time. The District had previously tried making this kind of repair by wrapping stainless steel bands around the affected pipe but found that the high water pressure would blow out the seals once regular service resumed.
The Challenge
To repair the pipe quickly and securely while minimizing service downtime – without cutting out the pipe.
The Solution
Linker decided to use a 12” HYMAX VERSA which was much stronger and easier to install compared to the stainless-steel repair bands. Instead of cutting out and replacing the pipe, an eight-hour job for two or three installers, the HYMAX VERSA was installed in about three hours with only two workers. There was no need to drain the water main, and Linker’s crew could maintain positive flow pressure without shutting it down completely. Water contamination was completely avoided, since the pipe wouldn’t have to be cut for the repair, and flushing was greatly reduced, saving time and water due to flushing. And in the long run, the VERSA’s stainless steel would withstand corrosion much better than a standard coupling.
“Using the HYMAX VERSA made the repair very easy both in terms of time and manpower,” said Linker. “When you can return service to customers faster and reduce the number of installers on the job, using the HYMAX VERSA was a good choice to make.”
HYMAX VERSA also offered a very durable solution. Its weld-free construction and 100% stainless steel parts made it resistant to corrosion, a key benefit given the surrounding hot soil. HYMAX VERSA uses the same coupling gasket in Hymax’s HYMAX coupling, which features a patented hydraulic pressure-assisted gasket that inflates as water pressure increases. This allows for three degrees of dynamic deflection on each end to reduce the risk of future damage to the pipe due to ground shifts and temperature changes. The radial closing design and sealing systems also help eliminate installation errors.